Where the refrigerant is essential for the cooling properties of a refrigeration system, the refrigeration oil is crucial for the correct functioning of the compressor. Lubricants for refrigeration compressors reduce friction, prevent wear and act as a seal between the high and low pressure sides. But how do you select the best refrigeration oil?
Although the primary function of refrigeration oil is still lubrication, it should also be able to withstand extreme temperature differences and be compatible with the refrigerant.
How does a refrigeration system work?
The most common refrigeration cycle is accomplished by circulating, evaporating, and condensing the refrigerant in a closed system. Evaporation occurs at low temperature and low pressure while condensation occurs at high temperature and high pressure. This makes it possible to transfer heat from an area of low temperature to an area of high temperature. An overview of this refrigeration cycle is shown in Figure 1.
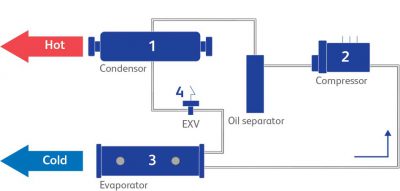
- Hot compressed vapour enters the condenser where it is cooled and condensed into a liquid, heat is generated.
- Refrigerant enters the compressor in the vapour phase and is compressed to a higher pressure, resulting in a higher temperature.
- The cold mixture enters the evaporator. The liquid part of the cold refrigerant mixture is evaporated.
- Condensed liquid refrigerant flows through an expansion valve where the pressure is reduced. The pressure reduction results in the evaporation of a part of the liquid refrigerant. This lowers the temperature of the liquid and vapor refrigerant mixture.
Which refrigerants are used for refrigeration systems?
- CFC (Chloro-Fluoro-Carbon): these refrigerants are most harmful to the ozone layer. Examples: R11, R12, R13, R13b1, R14, R113, R114 and R115.
- HCFC (Hydro-Chloro-Fluoro-Carbon): these refrigerants are slightly harmful to the ozone layer. Examples: R21, R22 and R123.
- HFC (Hydro-Fluoro-Carbon): these refrigerants are not harmful to the ozone layer. Mineral oil, PAO or alkylbenzenes are not compatible with HFC. Examples: R134a (used in car air-conditioning systems) and R152a.
- Ammonia (R717 (NH3): Although ammonia is environmentally friendly, pure ammonia gas is highly toxic to people. Ammonia is used extensively in large industrial refrigeration plants.
Mixtures of CFC, HCFC and HFC refrigerants are also available in the market. Examples of such mixtures are: R500 (=R12/R152a), R501 (=R22/R12) and R502 (R22/R115).
How to select the appropriate refrigerant?
The most important properties of refrigerants are:
- boiling point
- heat required to vaporize the liquid
- densities in liquid and vapour phase
Selection of the right refrigerant is mainly based on the suitability of its pressure-temperature relationship in the range of the particular application. The temperatures of the refrigerant in the evaporator and condenser are the temperatures of the cold and warm sections. This determines the operating pressures in the evaporator and condenser.
Refrigeration oils requirements
1. Thermal stability
Refrigeration oils must function correctly over a wide temperature range. End compression temperatures in refrigeration compressors can reach peak temperatures of up to 180ºC. Therefore the refrigeration oil must be thermally stable. If the oil contains volatile oil fractions, the lighter ends enter the compressor system as vapour where they condense and reduce the heat transfer efficiency, but also increase the oil viscosity.
2. Chemical stability
Refrigeration oils should be chemically stable to avoid reaction with the refrigerant.
3. Refrigerent/oil solubility
Refrigerant/oil mixtures can be (partly) soluble or insoluble. Complete solubility facilitates lubrication but can lead to significant viscosity drops in the compressor which increases friction and wear. Table 1 gives an overview of various refrigerants available on the market and their solubility properties in combination with mineral oil (Q8 Stravinsky N).
Completely soluble | High
solubility |
Average solubility | Low
solubility |
Not
soluble |
R11
R12 R21 R113 R500 |
R13b1
R501 |
R22
R114
|
R13
R14 R115 R152a R502 |
NH3
CO2 |
Table 1: Solubility of refrigerants in mineral oil (Q8 Stravinsky N)
In order to function properly, the oil/refrigerant mixture should have a viscosity that is sufficiently high to give satisfactory sealing and lubrication in the compressor.
How to read a viscosity-temperature diagram?
Figure 2 shows the viscosity-temperature diagram of different mixtures of Q8 Stravinsky 68 and R22. The figure shows that the viscosity can drop significantly, even at low levels of refrigerant in the mixture. Too low a viscosity leads to increased friction and wear. Anti-wear additives are usually not used within refrigeration oils as there is a risk of reaction between additives and refrigerant.
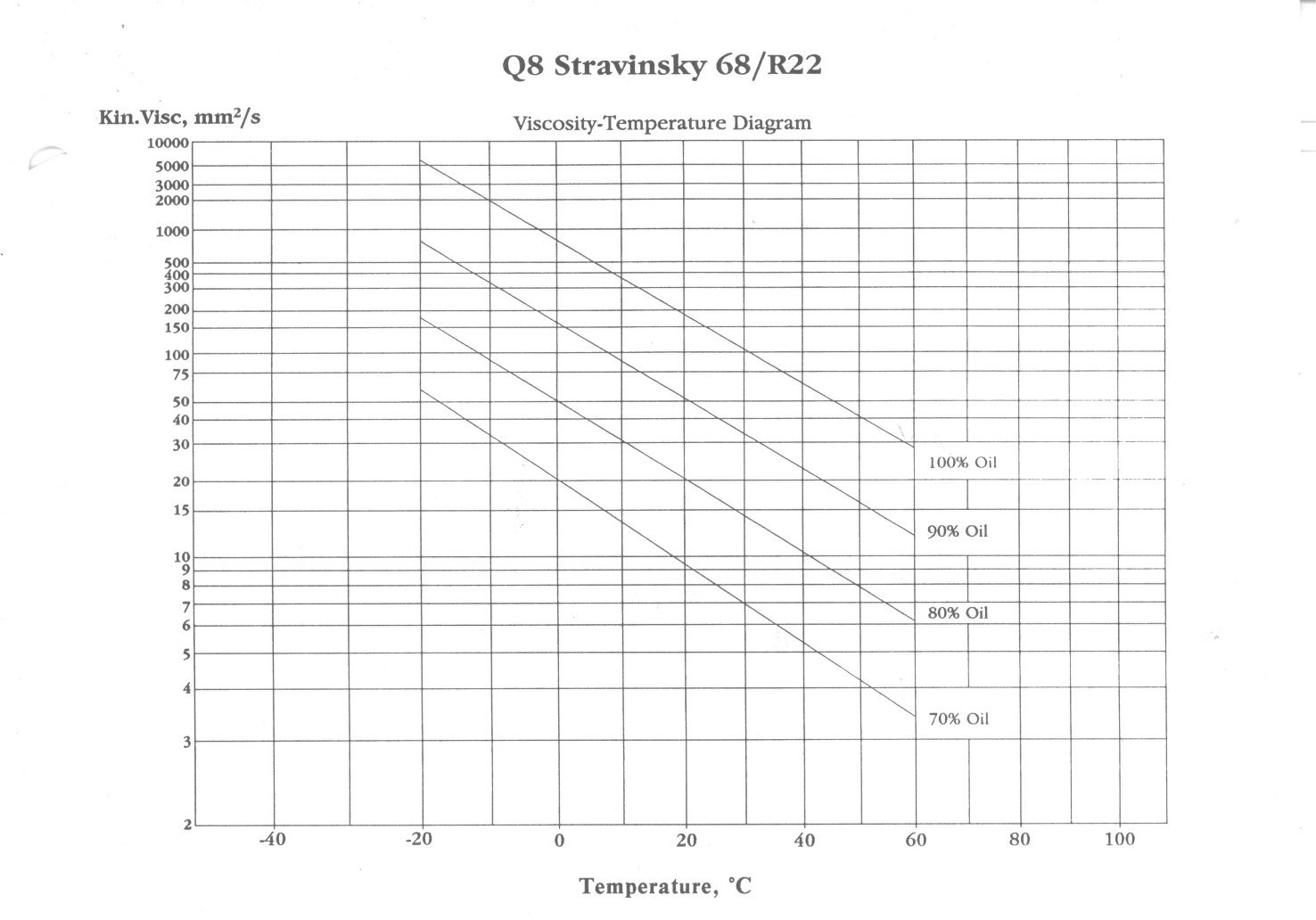
How to read a solubility diagram?
The solubility of Q8 Stravinsky 68 and R22 depends upon temperature and oil concentration. This means that Q8 Stravinsky 68 and R22 do not mix over the whole pressure and temperature range. When a fully dissolved refrigerant/oil mixture is cooled, a point will be reached when the fully dissolved mixture will separate into two liquid phases. This is shown in the solubility diagram (Figure 3). At temperatures higher than a given point on the line the two substances are soluble, below the line there is separation.
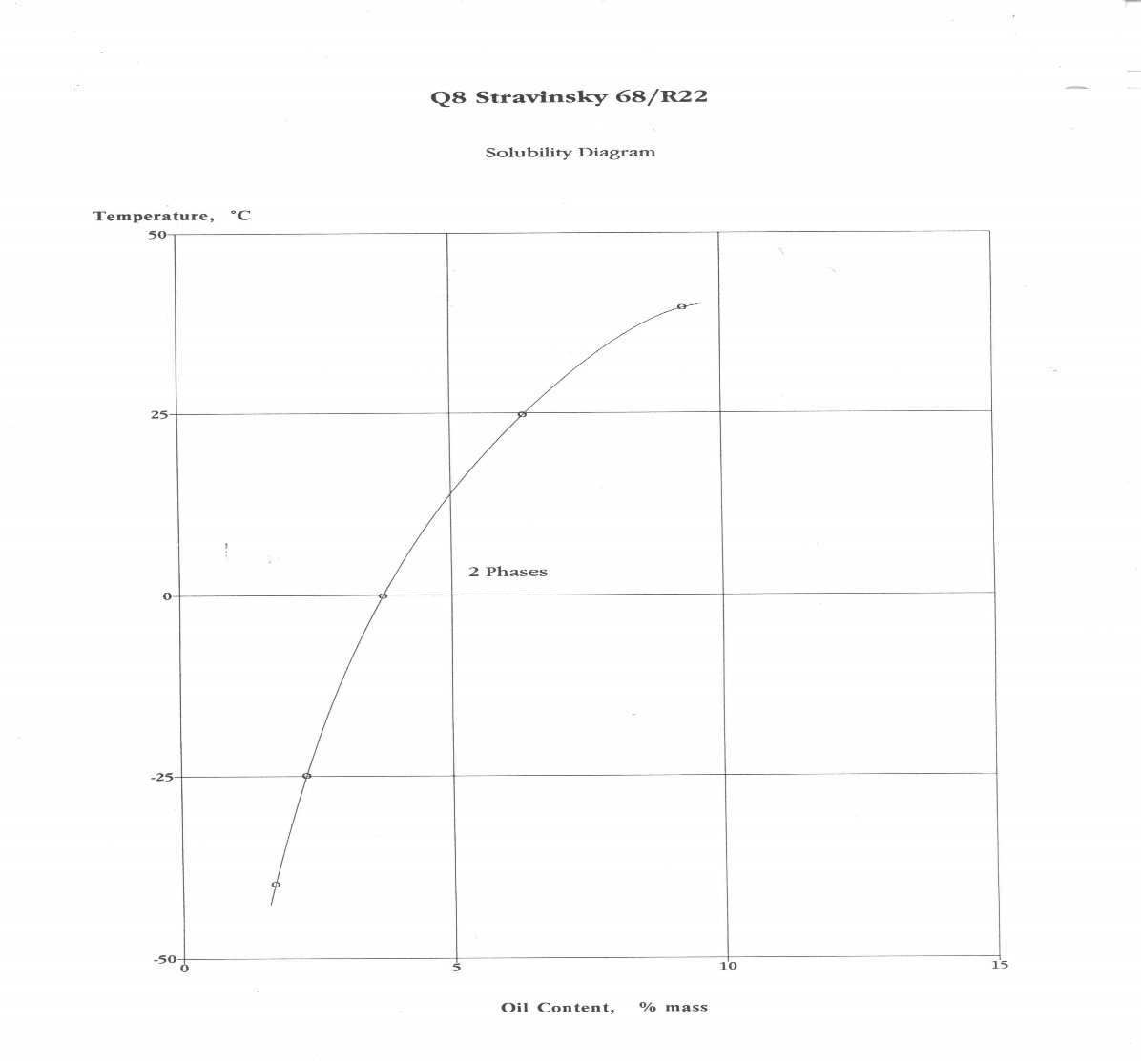
Figure 3: Solubility diagram for Q8 Stravinsky 68/R22 mixtures
4. Vapour pressure
When a liquid boils, the added heat is used to increase the kinetic energy of the molecules until they can no longer remain in the liquid phase and shift to form a vapour (or gas). This happens at a certain pressure, but if the pressure is raised the boiling temperature will increase too.
The relation between pressure and boiling temperature for saturated conditions (liquid and vapour) is defined as the vapour pressure diagram.
How to read a vapour pressure curve?
In figure 4 the pressure-temperature diagram for different saturated mixtures of Q8 Stravinsky 68 and R22 are shown. The liquid phase is to the left of the curve and the vapour phase (gas) to the right of the curve. The liquid can be vaporized either by increasing the temperature or decreasing the pressure. The vapour pressure curves are important as these curves in part define the conditions of the intended refrigeration system.
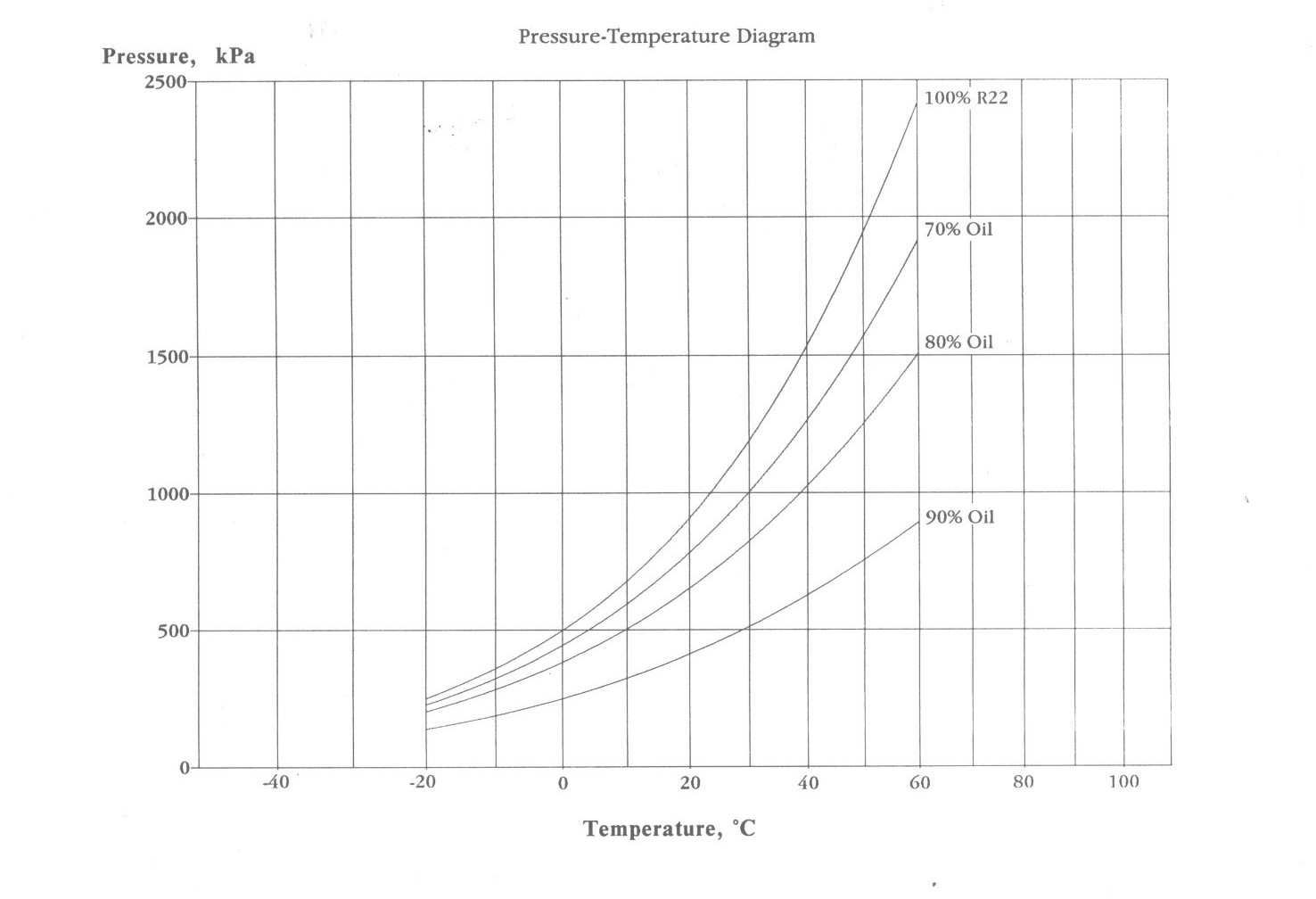
Figure 4: Vapour pressure curves for Q8 Stravinsky 68/R22 mixtures
You can use the above vapour pressure curves to determine what the pressure will be for an evaporating or condensing process, which is the basic principle of the vapour-compression cycle. When a liquid boils, it extracts heat from its surroundings. If the vapour thus produced is transported to a new location and compressed to a higher pressure, it can be condensed at a correspondingly higher temperature, releasing its heat of condensation to the new surroundings.
Which oil types are used for refrigeration systems?
- Alkylbenzenes (AB): these refrigeration oils have a good thermal and chemical stability. The miscibility with refrigerant is high. Alkylbenzenes are completely soluble with mineral oils and PAO, which makes it possible to produce mixtures in order to improve the lubricant properties.
- Polyalphaolefin (PAO): these refrigeration oils have a good chemical and thermal stability. PAO also has excellent viscosity temperature characteristics. The miscibility with refrigerant is low, which is why the major use of PAO in refrigeration is in applications where miscibility is not a concern. PAO can cause seals to shrink, which can be solved by mixing PAO with AB.
- Polyol ester (POE): this refrigeration oil is the most common type of synthetic lubricant being used with HFC refrigerants, like R134a.
- Polyalkyleneglycols (PAG): these refrigeration oils have a high viscosity index and thermal stability. However, PAG is hygroscopic, which means it can attract water. PAG is soluble with ammonia.
- Mineral oil: Naphtenic oils have a low pour point, which make them more suitable at lower temperatures.
Q8Oils range of refrigeration oils
Q8Oils has a full product portfolio available. The range is based on Naphtenic, Alkylbenzenes, mixtures of PAO and Alkylbenzenes, and synthetic Polyol Esters.
Conclusion: carefully select your refrigeration oil
Selection of the correct refrigeration oil depends on the specifications of the compressor and the refrigerant that is being used.
The refrigeration oil should be chemically and thermally stable and not react with the refrigerant. Also very important is how the refrigeration oil interacts with the refrigerant (e.g. solubility properties) and how the mixture performs in the compressor. Lubricant related problems can occur in a refrigeration compressor when the lubricant viscosity becomes too low or when there is absence of oil.