Visit Q8Oils at stand 11 B16 at Wire & Tube 2020 to discuss its many products and service-led initiatives available for the worldwide wire, tube and cable market.
Q8Oils at Wire & Tube 2020
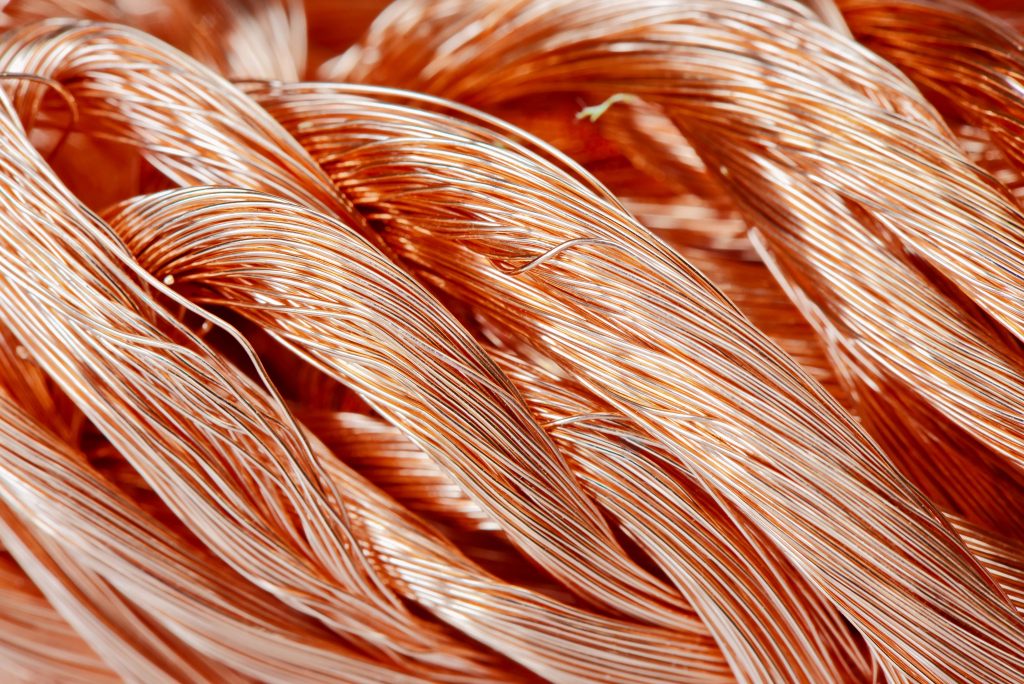
Visit Q8Oils at stand 11 B16 at Wire & Tube 2020 to discuss its many products and service-led initiatives available for the worldwide wire, tube and cable market.
Q8Oils has launched its most advanced range of cutting oils – Q8 Bach 7000 – which break the boundaries in performance and safety.
In August, Q8Oils visited Freddy Products Ltd, the manufacturer of the highly regarded and world-renowned Freddy range of coolant and swarf recycling vacuums.
Q8Oils is a key player in the metalworking industry and develops a wide product range of metalworking fluids, allowing our customers to choose the perfect solution for their process and application. Our strategic pillar of metalworking fluids increases the profitability and sustainability of big and small companies worldwide.
At Q8Oils, the answer is quite a lot! We have produced a paper to give you the key facts about aluminium, from its properties and classification to important considerations in the machining process.
Stainless steel is often considered difficult to machine. While using the right machinery and tools for the job is most important, choosing the most effective metalworking fluid can help overcome common machining problems.
Getting the most from your metalworking fluid is all about choosing the correct equipment. Using the right equipment makes it possible for you to enhance the life of your fluid, improve its longevity and prevent problems in the future. So, what equipment should you use?
Our first priority is the health and safety of the machine operator and other people within the vicinity of the machine. Our Q8 Brunel range is designed to provide the optimum balance of protection against microbiological contamination without the need for using unnecessarily harmful chemicals providing a safe working environment.
Q8 Brunel XF 527 is an advanced non-cobalt leaching synthetic grinding fluid developed to give the highest quality finish in all operations. It contains no mineral oil and is free from boron, formaldehyde, nitrite and secondary amine. When diluted with water it forms a true solution rather than an emulsion which gives excellent wheel and work piece visibility. Q8 Brunel XF 527 uses the latest in fully synthetic anti-corrosion additive technologies and has outstanding corrosion protection, suitable for all ferrous metals giving rust and stain free machining.
The cobalt that is released into metalworking fluid (MWF) as a result of the shaping and sharpening processes may dissolve and circulate in the fluid or become sediment at the bottom of the filter into which it was released.