The main circulation lubricant in industrial applications comes into contact with anti-rust fluids and sealants used to prevent leakages. Q8Oils has tested and analysed how these products affect lubricant anti-wear properties
In order to understand what could happen if the system is not properly flushed before start-up and if excessive amounts of sealant are used, Q8Research has investigated this issue.
The influence of rust-preventive fluids
To investigate the effects of rust preventive fluids on lubricant performance, Q8Research has evaluated a fluid that is being used in the paper making industry. This product is used to prevent rust and corrosion during storage of the paper machine parts and during assembly, predominantly to protect the bearings. Although the paper machine is flushed after assembly, some of the rust preventive fluid can still remain inside the system.
Based on the experience of a paper machine OEM the tests were done on mixtures of 0.5%-mass and 3.0%-mass rust preventive fluid with Q8 Vermeer WD 220.
Results
The test results are partly shown in the table below.
Test | Method | Unit | Q8 Vermeer WD | Q8 Vermeer WD + 0,5%-mass rust preventive | Q8 Vermeer WD + 3.0%-mass rust preventive |
Appearance, Visual | KPI 70 | – | bright and clear | bright and clear | bright and clear |
Appearance, Visual, | KPI 70 | – | bright and clear | bright and clear | bright and clear |
Air Release @ 75 °C | ASTM D 3427 | min | 9 | 10 | 11 |
Water seperability @ 82 °C | ASTM D 1401 | ||||
Oil Phase | ml | 40 | 40 | 40 | |
Water Phase | ml | 40 | 40 | 40 | |
Emulsion Phase | ml | 0 | 0 | 0 | |
Separation Time | min | 10 | 15 | 15 | |
Foaming Characteristics | ASTM D 892 | ||||
5 min blowing, seq. I | ml | 0 | 5 | 0 | |
10 min settling, seq. I | ml | 0 | 5 | 0 | |
Kinematic Viscosity @40°C | ASTM D 445 | mm2/s | 220.7 | 218.5 | 210.5 |
- The appearances of the mixtures remain bright and clear, indicating that rust preventive fluid is chemically compatible with Q8 Vermeer WD 220 up to a treat level of 3%-mass.
- The air release and water separability show a slight decrease in performance when the amount of rust-preventive fluid is increased. However, the performance of the mixture is still within OEM specification and the decrease in test performance is still within test repeatability.
- Foam test results on the mixtures do not indicate that the foaming properties of Q8 Vermeer WD are much affected by the rust preventive fluid.
- Please note that the kinematic viscosity at 40°C is reduced due to the presence of the rust preventive fluid. This is to be expected as the kinematic viscosity of the rust preventive fluid is approximately 50 cSt at 40°C, which is much lower than the 220 cSt of the paper machine oil.
Oxidation stability
The resistance against oxidation of the mixture is shown below and compared to the fresh oil value of 100 %.
The oxidation stability can be affected when rust preventive fluid is mixed with Q8 Vermeer WD. However, this does not necessarily mean that the rate at which the oil ages, is increased as well, but caution is required.
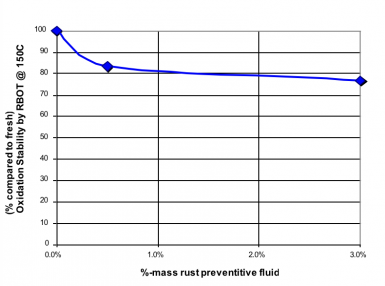
Wear resistance
Four ball wear testing was done in order to evaluate the influence of the rust preventive fluid on the wear protection performance of the paper machine oil. The results are shown in the graph below.
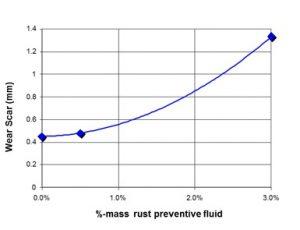
The rust preventive fluid can significantly influence the wear protection properties of the paper machine oil. This effect is small when the amount of rust preventive fluid in the paper machine oil is small (e.g. <1%), but can be significant when the amount increases. The reason is probably that the rust preventive chemistry is also a surface-active material competing with the anti-wear additives.
The influence of sealants
To investigate the effect of sealants on lubricant anti-wear performance Q8 Research has evaluated a sealant based on acetoxy silicone. It is used in gas- and steam turbines where Q8 van Gogh and Q8 van Gogh EP could be in the system as lubricant. When excessive amounts of sealant are used there is a risk that some sealant could enter the lubrication system.
Results
The anti-wear properties were tested with the four ball wear test (acc. to ASTM D 4172). Tests were done with and without sealant in the lubricant.
The test results are shown in the table below.
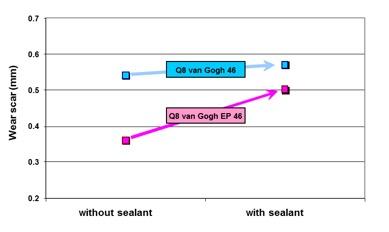
As sealant and lubricant are not soluble, the test with sealant was done by adding an excessive amount of sealant to the lubricant. Although it could be questioned whether this is comparable to practice, it does indicate what may happen if the conditions are wrong.
Conclusion
Although rust preventive fluids and sealants can be chemically compatible with lubricants, under specific conditions (e.g. excessive amounts/residual volume) lubricant performance properties such as anti-wear can be influenced. The reason is probably that sealants, rust preventive fluids and anti-wear chemistry are active on the same surface, therefore reducing each other’s effectiveness.
As a result of our testing, we have a better insight in how anti-rust fluids and sealants impact lubricant performance. It helps Q8Oils in giving better advice and service to customers.
For questions about the compatibility and miscibility of two products, please contact the technical support department of Q8Oils.