Product information
Q8 Brunel XF 527 is an advanced non-cobalt leaching synthetic grinding fluid developed to give the highest quality finish in all operations. It contains no mineral oil and is free from boron, formaldehyde, nitrite and secondary amine. When diluted with water it forms a true solution rather than an emulsion which gives excellent wheel and work piece visibility. Q8 Brunel XF 527 uses the latest in fully synthetic anti-corrosion additive technologies and has outstanding corrosion protection, suitable for all ferrous metals giving rust and stain free machining.
Application
Q8 Brunel XF 527 is recommended for all hard metal machining including Tungsten Carbide. It is formulated with a special inhibitor to prevent the leaching of cobalt into solution.
It is suitable for all grinding operations including, surface grinding, cylindrical grinding (internal and external), as well as tool and cutter grinding. It is particularly recommended for creep feed and centreless operations.
What is carbide grinding?
Carbide is made by combining carbon with a powdered metal such as tungsten or titanium using cobalt to bind together like cement. This creates an extremely hard material used in tooling to machine hard super-strength alloys and provide extreme tool life and surface finish Since this composition is so hard diamond wheels are often used for grinding in order to shape the tool. It is therefore essential during grinding to select the most suitable coolant to provide optimum cooling, and corrosion protection. It is more essential however to select a coolant / MWF that can resist the leaching of cobalt during the machining of the tool.
What is cobalt?
Cobalt is a chemical element with symbol Co and atomic number 27.
It is a highly useful element used for the manufacture of magnetic, wear-resistant and high-strength alloys and also as a catalyst in many chemical processes. Cobalt is also an essential element for the human body in very small amounts (ppb) as the active centre in cobalamin, a coenzyme group better known as vitamin B12. This plays a vital role in the functioning of the nervous system.
However at higher levels (> ppm) cobalt is harmful to humans through exposure via ingestion, inhalation, contact with the skin.
Exposure levels of cobalt
OSHA has an exposure limit of 0.1 milligrams of cobalt per cubic meter of air in the workplace atmosphere for an eight hour work day (40 hour week). The National Institute of Occupational Safety and Health (NIOSH) have recommended occupational exposure limits of 0.5 milligrams of cobalt per cubic millilitre of air in a 10 hour work day (40 hour week).
Why use Q8 Brunel XF 527?
Q8 Brunel XF 527 contains a special blend of additives to deliver both machining performance and be able to inhibit the leaching of cobalt from carbide machining into the fluid. This has been tested using the most sophisticated analytical techniques after exposing the diluted product to cobalt under experimental conditions. As well as being non cobalt leaching Q8 Brunel XF 527 is free from formaldehyde & boron providing a high performing fluid with an excellent health and safety profile.
Non cobalt leaching
A selection of water mix grinding and machining fluids were tested at 5% dilution. 1 gram of cobalt powder was added to each dilution and shaken once everyday over a period of 14 days. The solutions were filtered and analysed for dissolved cobalt by ICP-AES.
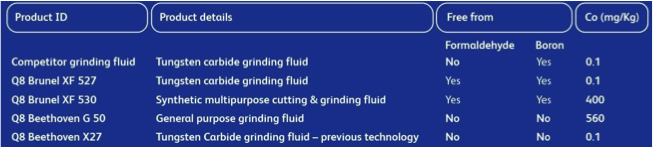
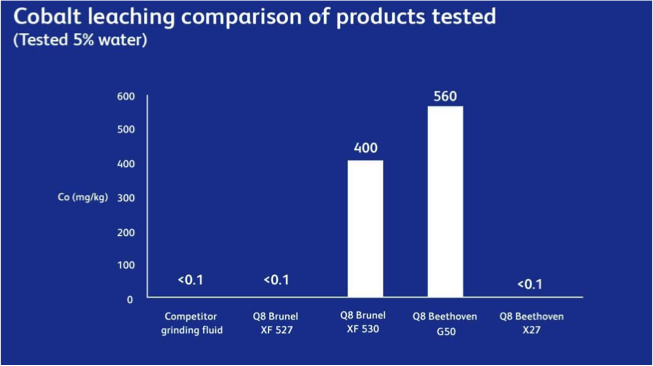
Benefits of Q8 Brunel XF 527
- Free from boron, boric acid, formaldehyde, chlorine, sulphur & secondary amine
- Avoids the hazards associated with cobalt leaching
- Used at low concentrations so cost effective
- Very good anti-corrosion properties
- Easily maintained, has excellent filterability
- Stable in all water conditions
- Very clean product in use
User instructions
Recommended concentration
General grinding
3.5 – 5.0%
Steels and hard carbide materials grinding
5.0 – 6.0%
In certain applications it may be beneficial to run at higher concentrations than those stated.
Typical properties
Properties | Method | Unit | Typical |
Appearance neat | Visual | Pale yellow fluid | |
Density 20°C | g/ml | 1.10 | |
Corrosion Test | IP 287 | % | 3.0% Breakpoint |
Refratometer factor | 1.4 (reading x factor = true concentration) |