This series of articles focuses on five aspects of emulsions for copper wiredrawing that manufacturers must focus on to maximize their productivity and reduce production costs.
Lubrication consistency
Lubrication consistency with newer generation copper wiredrawing lubricants can be demonstrated and proven with both laboratory analyses and in live factory applications. Under controlled identical conditions, product technologies can be cross-referenced and compared in KPI’s laboratories. Artificial aging is done by a set criteria of excessive heat, copper fines, air blowing and hard water providing very stringent conditions for wire drawing emulsion evaluation. The unique co-efficient of friction equipment being used to determine the wire to capstan lubrication film performance is used through the emulsion testing.
This test method uses wiredrawing equipment to measure a drawing emulsion’s lubricating performance and thus can be considered a more powerful result than more traditional oil industry lubrication test methods, such as Falex or Reichert. The results from this artificial aging process can demonstrate differences from one wiredrawing lubricant technology to another. It is possible to calculate the theoretical lifespan of the wiredrawing emulsion. The lubrication level is also monitored to determine if performance is consistent throughout the emulsion life. This is compared with the tail-off in lubrication performance commonly seen with lesser quality products. Fig. 4 shows the COF machine and Fig. 5. shows a data chart.
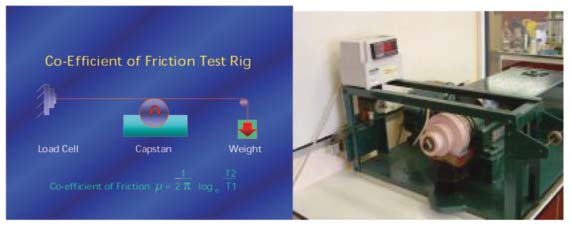
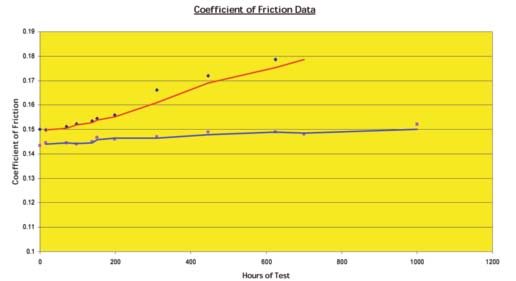
Housekeeping and performance
All soluble oil concentrates should be stored indoors and protected from extreme temperatures of frost and direct sunlight. The drums should be stored to avoid water ingress as this will harm the concentrate. The ideal storage position is to place the drums on their side with bungs at the quarter to three position.
Mixing
The emulsion mixing process can also affect the long-term stability and lifespan of the wiredrawing emulsion, so it is vital to always add the concentrate to the water rather than the other way around to avoid instability. Mixing units are recommended, especially positive-displacement mixing units that will inject the concentrate into the water. See Fig. 6.

Water
The water quality used for make-up is important for the life and long-term stability of the wiredrawing emulsion. The water should have medium hardness for emulsion make-up and low hardness for emulsion top-up. It is also beneficial in certain applications to use demineralized water. Please note that the use of salt softened water is not recommended as the salts which form the hardness are replaced by further salts that can cause increased conductivity levels in the emulsion which can reduce the emulsion life.
Machine Cleaning
The procedure for cleaning machines and preparing machines for emulsion fill is important for removal of debris, fines and deposits in used systems and also for removal of corrosion protective in new machines as these can promote initial emulsion foaming.
Housekeeping and maintenance
Emulsions should be maintained at the correct concentration. In a training scenario, “Milk” is used as an analogy. Milk is an emulsion of fatty oil in water; if left uncared for it can become infected with bacteria, fungi or yeast and separate into layers. Thus, it is important to protect wiredrawing emulsions from biological contamination as ultimately this will save money and create a safer working environment.
Precautions for wiredrawing emulsions
Keep the drawing emulsion above the minimum recommended concentrations and use a refractometer to record the concentration. Sterilize and clean the system before introducing a fresh emulsion. Avoid contaminated water during emulsion make-up. Do not discard waste items, either food or human, into the emulsion as this will cause severe bacterial infections. Minimize metal fines by effective emulsion filtration. Keep the emulsion temperature between 35°C and 45°C, and avoid tramp oil contamination. Simple measures and general monitoring of emulsion condition can increase emulsion life, save costs and improve the working environment of the drawing machine. This results in cleaner drawing dies and longer die life, a cleaner machine and increased speed and machine output. The above points save money by simple techniques often overlooked by wiredrawing companies. The emulsion may be the smallest cost item of the wiredrawing process, but it is the most influential to machine productivity.
Emulsion performance
Throughout the wiredrawing emulsion life the factory should monitor and record production data and keep records of the emulsion condition monitoring and maintenance. The consumption rate of emulsion can be measured and then used as a benchmark target to install a procedure of operator “ownership” of the machine and wiredrawing emulsion performance. Data of tonnage drawn, top-up rates, wire-break analysis and emulsion analysis should be recorded and monitored. One such service is “Roloil Fluid Care” a high-quality maintenance program offered by Roloil that is known as “Technical Service on the Move.” See Fig. 7. Typical consumption rate for a process should 0.1 to 0.25 liters emulsion per metric ton of copper wire drawn. This rate depends on emulsion chemistry and working practice of the factory as every system will have its own figure.
